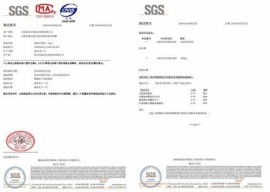
1. Carbon (C): carbon content in steel increases, the yield point and tensile strength increased, but lower ductility and impact resistance, when the carbon content exceeds 0.23%, weldability deteriorate, resulting in low alloy for welding structural steel, carbon content generally less than 0.20%. It also reduces the amount of carbon steel, high resistance to atmospheric corrosion, high-carbon steel on the open-air yard easily corroded; addition, carbon can increase sensitivity to cold brittleness and aging steel.
2, silicon (Si): Si added as a reducing agent in the steel making process and the deoxidizer, it is killed steel containing 0.15 to 0.30% silicon. If the steel is 0.50-0.60% silicon content than silicon even alloying elements. Silicon can significantly increase the elastic limit of the steel, the yield point and tensile strength, it is widely used as a spring steel. 1.0-1.2% silicon was added in the quenched and tempered steel, the strength can be increased by 15-20%. Silicon and molybdenum, tungsten, chromium, combined with improving corrosion resistance and antioxidant effects, can produce heat-resistant steel. Silicon 1-4% of low-carbon steel, with a high permeability silicon steel for electrical industry do. Silicon content increases, decreases weldability.
3, manganese (Mn): In the steelmaking process, the manganese and the deoxidizer is a good desulfurization agent, typically 0.30-0.50% manganese steel. In carbon steel added 0.70 percent or more, even if “manganese” steel than the average amount of steel not only have enough toughness and high strength and hardness, improved steel quenching, improved hot workability of steel, 40% higher than the A3 as 16Mn steel yield point. 11-14% manganese steel has high resistance to abrasion, *** bucket for digging, milling, etc. *** liner. Manganese content increased, decreased corrosion resistance of steel to reduce welding performance.
4, phosphorus (P): In general, phosphorus is harmful elements in steel, an increase of cold brittleness of steel, welding performance deterioration, reduce plastic, so cold bending performance deterioration. Therefore, the amount of phosphorus in steel usually require less than 0.045%, high quality steel requires lower.
5, sulfur (S): Sulfur is usually in harmful elements. Generating hot brittleness of the steel, to reduce the ductility and toughness of the steel, resulting in cracking during forging and rolling. Sulfur is also detrimental to the welding performance and reduce corrosion resistance. So often require the sulfur content of less than 0.055 percent, less than 0.040% high quality steel requirements. Adding 0.08-0.20% sulfur in the steel can be improved machinability, usually called cutting steel.
6, chromium (Cr): structural steels and tool steels, the chromium can significantly increase the strength, hardness and wear resistance, but lower ductility and toughness. Chrome steel can improve the oxidation resistance and corrosion resistance, so it is stainless steel, heat resistant steel alloying elements is important.
7, nickel (Ni): Nickel can improve the strength of steel, while maintaining good ductility and toughness. Nickel acid have a higher corrosion resistance at high temperatures rust and heat capacity. But because nickel is relatively scarce resource, it should be possible to use other alternative alloying elements nickel chrome steel.
8, molybdenum (Mo): Molybdenum steel grain refinement can improve the hardenability and heat resistant properties, while maintaining sufficient strength at high temperatures and creep resistance (long-term at high temperatures is subjected to stress, deform, said creep). Mo added steel structure, can improve the mechanical properties of ***. You can also inhibit brittle alloy due to the fire caused. In the tool steels can increase red sex.
9, titanium (Ti): Ti is a strong deoxidizer in steel. It enables the internal organization of the steel dense grain refinement force; reduce aging sensitivity and cold brittleness. Improve welding performance. Adding a suitable nickel-titanium in 18 9 of chromium in the austenitic stainless steel, intergranular corrosion can be avoided.
10, Vanadium (V): Vanadium is an excellent steel deoxidizer. Steel added 0.5% vanadium can be refined grains organization, improve the strength and toughness. Vanadium carbide and carbon formed under high temperature and pressure can increase resistance to hydrogen corrosion.
11, tungsten (W): tungsten melting point higher than the major, students are expensive alloying elements. Tungsten carbide and carbon formation has a high hardness and wear resistance. Plus tungsten in tool steel, can significantly increase the red hardness and heat resistance, as cutting tools and forging mold.
12, niobium (Nb): Niobium can refine the grain and reduce the thermal sensitivity and temper brittleness of steel, improve strength, ductility and toughness but declined. Niobium in the general low-alloy steel, you can improve the anti-hydrogen, nitrogen, ammonia corrosion resistance to atmospheric corrosion and high temperature under. Niobium can improve the welding performance. Increase in austenitic stainless steels, niobium, among prevents corrosion phenomenon.
13, cobalt (Co): Cobalt is a rare precious metal, used for special steels and alloys, such as heat resistant steel and magnetic materials.
14, copper (Cu): Wuhan Iron ore by smelting with Daye Steel, often contain copper. Copper can improve the strength and toughness, especially to atmospheric corrosion. The disadvantage is likely to generate heat during hot working embrittlement significantly reduces the copper content exceeds 0.5% plastic. When the copper content is less than 0.50% has no effect on the weldability.
15, aluminum (Al): Al is a deoxidizing agent in steel used. Steel adding a small amount of aluminum, refined grains can improve the impact toughness, such as deep-drawing steel sheet 08Al. Aluminum also has antioxidant and anti-corrosion, aluminum and chromium, silicon combination, can significantly improve the ability to afford high-temperature steels and high temperature corrosion performance skin. The disadvantage is the effect of aluminum thermal processing properties of steel, weldability and machinability.
16, boron (B): a small amount of boron can be added to steel to improve the density of the steel and hot-rolling properties, to improve the strength.
17, nitrogen (N): nitrogen can improve the strength of steel, low temperature toughness and weldability, increasing aging sensitivity.
18, RE (Xt): refers to the rare earth element of atomic number 57-71 in the Periodic Table 15 lanthanides. These elements are metal, but their oxides are like “earth”, so called rare earths on the habit. Steel added rare earth, can change the composition of inclusions in steel, morphology, distribution and nature, thereby improving the various properties of steel, such as toughness, weldability, cold performance. Plowshare adding rare earth in steel can improve the wear resistance.