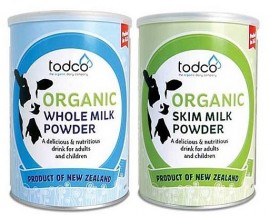
Canned container surface coating, it is in the tin before cutting into tank body blank with a proper coating roller coating machine will be painted on the tinplate smooth surface evenly, can control the thickness of the coating. The coating machine by itself independently with the feeding device of coating operation, can also be associated with YinTieJi form a complete set of seal coating line.
Turning of stainless steel half immersed in the feed roller feeding plate, will take up the coating after divide evenly feeding roller transfer to the rubber roller. Under the rubber roller have a impression cylinder, with smoking tooth device. When the tin before running to the rubber roller, embossing roller teeth in tight one end of the iron sheet, rubber roller and embossing roller and pushing tin, complete with homework. Addition, the thickness of the coating by the feeding roller, uniform roll and rubber between roller and embossing roll gap control. Because of the tin with space between zhang and zhang, so they have a small amount of coating was taken away by embossing roller. Scraper is used to change the impression cylinder shave their clean (avoid tin coated printed on the back of the pick-up), scrape the paint into the material plate, collected after transcatheter back into storage VAT and recycled.
Seam welding parts of the canned food containers cannot be printed on coatings, otherwise the body blank in the high frequency resistance breakdown seam welding process caused by the waste tank. As a result, the operator should according to canned container coating printing area on the rubber roller slot. Coating by slot rubber roller coating printing on tin, margin slot parts of iron is empty cans high-frequency resistance welding parts
We realized that in the actual operation, the size of the slot should be than actual welding blank size 1 ~ 2 mm wide, such coated printed blank size to conform to the requirements of the empty cans welding.
Coating after printing tinplate via conveyor belt shipped to the chamber, the loop runs chain driven by drying room temperature curing. Chamber is generally divided into three parts: the first part is the iron sheet preheated to the baking temperature; The second part is the constant temperature oven; The third part is to make the iron cooled sufficiently. The baking time take 10 ~ 15 min. Since version with automatic type discharge machine tin, into after coating is qualified through inspection, physical and chemical testing can process.