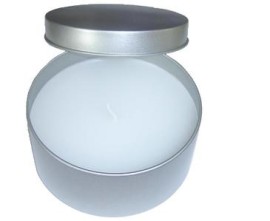
Plating pretreatment in electroplating production line is very crucial step in the electroplating process, the stand or fall of base material surface treatment directly affects the quality of the coating, so dealing with before electroplating processing is quite seriously. In this paper, the surface state of various factors affecting the quality of coating, electroplating production line before electroplating process of all kinds of basic methods.
The plating parts before plating processing is one of the most important factor in determining the quality of electroplating. In actual production, the electroplating failure rate more than 80% in the pretreatment process, so the stand or fall of plating pretreatment effect is particularly important, the following specific surface state of substrate on coating structure and the influence of the bonding force.
One, the influence of substrate surface state on the coating structure
Coating is made up of crystals or grains, crystal decides the size, shape and arrangement of the structure characteristics of the coating. In a variety of plating solution, the structure of the metal coating characteristics are also different, mainly due to different sedimentary process. Began to electroplating, surface of substrate material first generate some small dots, namely the crystal nucleus, with growth time, the number of single crystal increases, and connect with each other and form a coating.
Crystal nuclei grow up process, due to the characteristics of the matrix metal and operating conditions of different and different, mainly has the following several ways. If plating at the beginning of a lot of crystallization of nuclear generation, and continue to grow up, all is the formation of fibrous crystal, and vertical arrangement at the cathode surface; If the formation of crystal nucleus is only part of growing up, can appear the following two conditions: the crystal nucleus in the form of separate long needle (dendritic) to develop in the direction of anode and crystal nucleus grew up in three directions are evenly, because of the different, the growth rate of crystal nucleus of crystal nucleus the crystallization of the small crowd out, form is more and more thick conical crystal.
If plating start the crystallization of the generated quickly stop growing, while on the surface of the crystal and regenerate new crystallization, is the position of the crystallization of the this kind of circumstance may be chaotic, in cyanide electrolyte coating is the case. Coating structure except under the influence of electrolyte composition, process conditions, has seriously affected the surface state of substrate material. If there are mechanical impurity on the surface of substrate material, harmful to the coating organization; Were it not for electrolyte adhesion on the substrate material or coating, will form the hemp pit; If electrolyte stick on it, the formation of nodules. Clip these impurities in the coating, would also reduce the rust resistance of coating. If the surface of substrate material such as oil, scale, it is impossible to get a combination of strong coating; Base material surface is rough, it is difficult to get a light coating; Sometimes substrate material and coating causes tissue, crystalline pattern. Therefore, select the appropriate pretreatment process, the surface of substrate material about the quality of the galvanized coating has very important significance.
Second, the influence of the substrate surface state on coverage
The surface state of substrate material is one of the main factors influencing the coverage. Practice shows that metal electrodeposition on different substrate materials, the same coverage of plating solution is very large. If use chrome plating chromic acid solution, metal chromium deposition on copper, nickel, brass and steel, the coverage of decline in turn. This is because when the metal ions on the different substrate materials reduction deposition, its potential value have very big difference. Overpotential deposition potential is relatively small, even at the site of the low current density can achieve its deposition potential value, and its coverage is better. The surface state of substrate material on the influence of the coverage is more complex. In general, the same plating solution on the surface of the substrate that finish high coverage than its coverage on a rough surface. This is because the surface of the high degree of finish the real current density is high, easy to achieve the deposition potential of metal; And rough surface, because of the large surface area, the actual current density is low, not easy to achieve the deposition potential of metal, but related hydrogen. In addition, if the substrate surface treatment before plating, there is no “oil film, all kinds of film into a phase or dirt, etc., will also get in the way of coating deposition and reduce coverage.
Three, the influence of the substrate surface state on the binding force
Binding force, often referred to as an object to glue Jing the scope and degree of another object. If one falls off coating by mechanical force or deformation, or blown off by gas, or corrode and stripping, the lack of adhesion strength of coating. Binding force is one of the important performance index of electrodeposition, it and the surface state of substrate material in front of the plating have a very direct and important relationship, and binding force of the good or bad a direct impact on the coating quality.
If there is a lot of the surface of the substrate material oil, corrosion products, such as dirt, plating can not directly combined with base material surface, leading to a gradual peeling coating, fall off, etc., it is also a material surface coating and the magnesium substrate binding force because of the bad. On the contrary, if before electroplating, plating production line of the surface of the substrate material are well cleaning, plating will direct contact to the surface of the substrate material, and with the strong combination. And, of course, the metal ions on metal electrodeposition and many other factors, also state on the surface of the substrate material is not the only factor affecting the binding force, but it is the main factors influencing the bonding force.